восстановление позолоты
нанесение чистого золота
|
 Чистка медных предметов Секреты производственных технологий. Чистка медных предметов производится следующим образом: предметы из полированной меди вытирают сначала мягкой тряпкой, смоченной в керосине, а затем чистят шерстяной тряпкой порошком мела или. "венской" извести. Сильно запущенным медным предметам возвращают блеск, вытирая предмет тряпкой, смоченной разбавленной соляной кислотой. Затем чис-тят, как указано выше, или распускают в 1 литре воды 30 г щавелевой кислоты, добавляют 4 столовые ложки спирта и 3 столовые ложки скипидара. После этого жидкость хорошо взбалтывают и разливают в бутылки для хранения. При употреблении подлежащий чистке предмет слегка вытирают данной жидкостью, а затем вытирают сухой полотняной тряпкой: медь быстро вычищается и становится блестящей. Внимание: соблюдайте технику безопасности. Чистка никелевых предметов Секреты производственных технологий. Никелевые предметы, подлежащие чистке, смачивают сначала 2-3 раза смесью из 50 частей спирта (или водки) и 1 части серной кислоты; затем их споласкивают водой и, смыв спиртом (или водкой), вытирают тонкой полотняной тряпкой. Ржавчина на никеле удаляется следующим образом: смазать предмет каким-нибудь жиром и оставить так на несколько дней, затем тщательно вытереть нашатырным спиртом. Если ржавчина проникла глубоко, можно вместо нашатырного спирта взять разведенной соляной кислоты, которую, однако, оставляют на металле не более минуты. Затем предмет моют водой и полируют мелом и крокусом. Внимание: соблюдайте технику безопасности.  Предохранение железа от ржавчины Секреты производственных технологий. Предохранение это действительно в том случае, если поверхность была предварительно хорошо вычищена. Рекомендуются следующие средства: 1) Покрытие веществами, которые впитывают воду и кислоты или их связывают. Так, для предохранения от ржавчины паровых котлов на судах в воду добавляют раствор окиси цинка в едком натрии или твердую углекислую окись цинка. Кроме того, паровые котлы при их остановке наполняют известковым молоком или раствором соды. Лучше помещать в хорошо просушенные (при помощи топки) котлы хлористый калий кусками величиной с орех при одновременном прекращении доступа воздуха. В туннелях для предохранения железа от ржавчины применяется известняковый щебень или железные части покрываются известняковым молоком; этим достигается связывание и обезвреживание весьма вредного элемента, дающего ржавчину, а именно сернистой кислоты в дымовых газах паровозов. Гайки в туннелях дважды покрываются дегтем. 2) Покрытие металлом производится после предварительного вытравливания в кислоте и после быстрого высушивания в горячем состоянии; предметы погружаются в расправленный металл или покрываются гальванопластическим способом в соответствующей металлической ванне. Цинк - наилучший предохранитель (также и в морской воде), ибо в цинковой ванне на поверхности железа всегда образуется сплав железа с цинком. Оцинкованное железо в торговле часто встречается под названием гальванизированного. Лучше холодная электролитическая оцинковка. Олово предохраняет слабо и только до тех пор, пока железо нигде не обнажено. Свинец предохраняет от соляной и серной кислот: покрытые свинцом листы применяются для покрытия крыш химических, газовых заводов и т.п. Медь (гальваническая) и никель предохраняют лишь при значительной толщине слоя. 3) Эмалировка. Поверхность чугунной отливки вытравливается и высушивается, а затем покрывается порошкообразной грунтовкой (полевой шпат, кварц, бура и глина), обжигается до отекания и затем уже покрывается эмалью (силикаты с окисью олова) и нагревается до полного плавления эмали. 4) Жиры в твердом или жидком состоянии весьма удобны для покрытия чисто отделанных поверхностей машин до сборки. На открытом воздухе жиры смываются дождем или стекают от действия солнечных лучей. Сало с примесью 50-100% свинцовых белил также легко горкнет: образующиеся от распада нейтральных жиров жирные кислоты разъедают железо. Смесь талька с графитом рекомендуется для смазывания проволочных канатов (раз в месяц). В последнее время часто применяются минеральные жиры, растворенные в скипидаре или в легко летучих продуктах перегонки керосина. 5) Портландский цемент не только предохраняет от ржавчины, но вбирает в себя уже образовавшуюся на поверхности железа ржавчину (сооружения Монье). Цемент является также прекрасным средством для крупных отливок и больших железных сооружений. Мелко просеянный, разведенный в воде цемент наносится кистью на металлические чистые поверхности. Покрытие это повторяется от 4 до 5 раз после затвердевания последнего слоя. Для поверхностей, подверженных воздействию воды (шлюзы, дно судов), мельчайший цемент замешивается на снятом молоке. 6) Деготь, асфальт и смола в безводном состоянии служат хорошим покрытием для чугунных труб. Смола и трубы предварительно нагреваются. 7) Покрытие смоляными маслами. Каучуковое масло: раствор каучука в терпентинном масле. Антиоксид - слабый раствор гуттаперчи в бензине. 8) Резина и целлулоид дают прекрасное покрытие для гвоздей, винтов, пряжек, колец и т.п., и эти части тогда не подвергаются воздействию воздуха, воды, кислот. Это весьма важно для электрических изоляторов. Рекомендуется покрытие судовых валов твердой резиной. Части машин на судах дальнего плавания покрываются раствором целлулоида. 9) Покрытие масляными красками наиболее употребительно. Льняное вареное масло легко отстает; лучше для загрунтовки брать жидкое, быстро высыхающее льняное вареное масло, смешанное с графитом, охрой, железным суриком (не более 20% глины) или лучше со свинцовым суриком. Под водой хорошо оправдал себя только свинцовый сурик. После загрунтовки производится собственно окраска, для которой берут чистое вареное льняное масло со свинцовыми белилами (а не с цинковыми), графитом, цинковой пылью, а также с добавкой мела. Во избежание образования пузырей второй слой наносится лишь послеокончательного затвердевания предыдущего слоя. Внимание: соблюдайте технику безопасности.  Полировка железа Секреты производственных технологий. Подлежащие полировке железные изделия погружаются на некоторое время в смесь, состоящую из 1 части серной кислоты на 20 частей по объему воды, затем предмет вынимается, тщательно прополаскивается водой и высушивается в древесных опилках. После высушивания его тотчас же погружают на одну-две секунды в азотную кислоту, после чего вновь прополаскивают водой, вновь высушивают в древесных опилках и затем тщательно вытирают. При этом поверхность предмета становится блестящей, как стекло. Только вышеуказанным способом можно достигнуть такой совершенной полировки. Внимание: соблюдайте технику безопасности.
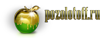
 Титановая живопись Ольга Максименко, ИнформНаука Рисовать можно угольком на скале, можно - краской на холсте, можно - мозаикой на стене, а можно - электричеством на титане, как придумали это делать московские ученые из Всероссийского института легких сплавов. Метод, который они разработали, официально называется "твердое цветное анодирование алюминиевых и титановых сплавов". Но это не просто новый способ наносить на металл удивительно прочное и устойчивое покрытие, хотя и тут есть элемент новизны - предложенный москвичами метод вдвое быстрее традиционных. Дело в том, что теперь защитный слой можно сделать еще и очень красивым, многоцветным, можно даже нарисовать на листе металла картину. В основе метода - хорошо знакомый еще по школьным урокам химии электролиз. Электролитическая ванна, анод, катод, как будто все известно. Но технологические тонкости - состав электролита, напряжение на электродах и некоторые другие детали, которые придумали доктор технических наук профессор Владимир Синявский и его коллеги, - позволили ученым сделать то, что не удавалось другим. Итак, в ванне - раствор кислоты, щавелевой или разбавленной серной. В нее погружают анод и катод. Катод обычный, угольный или свинцовый. Собственно изделие из титана или титанового сплава - анод. Под действием электрического тока на аноде выделяется кислород, который окисляет титан, и поверхность изделия покрывается пленкой - тонким слоем кристаллов оксида титана. Казалось бы, скучная рутинная процедура. Но у появившейся на титане пленки есть особенность - свет отражается от нее по-разному, в зависимости от ее структуры и толщины. Изменяя режим анодирования, в первую очередь напряжение, можно регулировать цвет пленки - от серебристой поверхности чистого металла через коричнево-золотистый к фиолетовому, проходя через все цвета спектра. Можно сделать титановую поверхность синей, голубой, зеленой, желтой, малиновой - какой угодно, любого цвета и оттенка, палитра безгранична. Если же использовать трафареты, то появляется возможность не просто раскрашивать поверхность в какой-то один цвет, но и наносить узоры - или рисовать настоящие картины. Такая висит, например, на стене кабинета профессора Синявского - это копия глазуновского "Летящего Икара". Необычно и, что называется, на века. Впрочем, у нового метода есть и более практичное применение. Например, строительные конструкции, которые не обязательно должны быть титановыми - метод работает и на алюминиевых сплавах, просто тогда в ванну с электролитом добавляют еще и соли титана. Если эти конструкции покрывают обычной оксидной пленкой толщиной около 20 микрон, на это уходит час, а "работает" она всего лет 8 - 12. Твердое цветное анодирование, разработанное москвичами, позволяет нанести защитное покрытие той же толщины всего за 20 мин, а долговечность его авторы оценивают не менее чем в 40 - 50 лет. Есть и другие области применения новинки - например, маркировка медицинских инструментов и титанового крепежа. А еще ювелирная промышленность: ведь легкие и красивые металлические штучки выглядят очень современно. Титан называют металлом XXI века за его прочность, стойкость и легкость. А теперь можно добавить - и за красоту.
ПРЕДЛАГАЕМ УСЛУГИ по НАНЕСЕНИЮ ПОЗОЛОТЫ, ВОССТАНОВЛЕНИЮ ЗОЛОТОГО ПОКРЫТИЯ --НАНЕСЕНИЕ ЗОЛОТА 999 пробы; --НАНЕСЕНИЕ РОЗОВОГО ЗОЛОТА 585 пробы; --ЗЕЛЁНОГО ЗОЛОТА; --НАНЕСЕНИЕ СЕРЕБРА; --нанесение ПАЛЛАДИЯ(БЕЛОЕ ЗОЛОТО); --ХРОМИРОВАНИЕ; --НИКЕЛИРОВАНИЕ; --НИТРИД ТИТАНОВОЕ ПОКРЫТИЕ; --МЕДНЕНИЕ; --ЛАЗЕРНАЯ ГРАВИРОВКА( В ТОМ ЧИСЛЕ И НА ЗОЛОТЕ); --РЕСТАВРАЦИЯ УКРАШЕНИЙ,ЧАСОВ. --РЕСТАВРАЦИЯ ОКЛАДОВ ИКОН. --ВОССТАНОВЛЕНИЕ ПОЗОЛОЧЕННЫХ И ПОСЕРЕБРЁННЫХ ЭЛЕКТРИЧЕСКИХ КОНТАКТОВ. --ИЗГОТОВЛЕНИЕ ЦЕРКОВНОЙ УТВАРИ. --ИЗГОТОВЛЕНИЕ ЛЮБЫХ ЮВЕЛИРНЫХ ИЗДЕЛИЙ. --ПОЗОЛОТА БРАСЛЕТОВ.
|

Уход за золотыми и позолочеными изделиями
При работе дома на кухне или выполнении других хозяйственых работ, особенно пользуясь бытовой химией, конечно рекомендую снимать часы и другие украшения.Это гарантия от повреждений и загрязнений. Так же не рекомендую контакт ювелирных изделий с пОтом,мыльной и стиральной пеной, различных духов и кремов. Пятна на золоте и других металлах могут остаться от соприкосновения с солями ртути и серы. Эти вещества могут находится в кремах, в дизельном топливе, в воде озера или пруда. От этих веществ появятся белые или тёмные пятна соответственно. Так же не допускайте поподания капелек кислот или йода. Они могут быть в лекарствах, пище, ну и в кислотных дождях))) Когда украшения имели соприкосновения с влажной кожей, протрите их при первой возможности сухой тряпочкой, смоченой в этиловом спирте. Сейчас продаются в аптеках такие. Но всё таки, лучше, время от времени, показывать свои бесценные сокровища ювелиру, дабы квалифицированно очистить и придать первоначальный блеск благородному металлу. Кстати сейчас существуют професиональные средства для долговременной защиты драгоценных металлов и сплавов от помутнений, окислений и мелких царапин. Но в применнении они довольно сложны, и требуют специального оборудования. Поэтому обращайтесь к ювелирам. Например к нам))) Поверьте это не дорого, но очень практично и сэкономит время и деньги.
 Уход за серебряными изделиями Не является тайной то, что даже чистое серебро темнеет под влиянием условий окружающей среды и требует периодической чистки. Серебро легко реагирует с сероводородом, особенно во влажной среде, покрываясь поверхностным «червленым серебром». А так как в воздухе постоянно присутствует сероводород, то на воздухе серебро со временем темнеет. Но не стоит унывать, что Ваше любимое украшение потеряло товарный вид. Привожу несколько способов, с помощью которых можно вернуть ювелирным изделиям блеск. -
Например, изделия можно промыть в теплой воде с питьевой содой (50г на 1 литр воды) или мыльной воде (либо моющее бытовое средство без отбеливающего эффекта) с нашатырным спиртом (1 ст. ложка на 1 литр воды). После промывки изделия ополаскивают и протирают насухо мягкой тканью. -
От пятен плесени на серебряных вещах можно избавиться, если потереть их тряпочкой, смоченной подогретым 6%-м раствором уксуса. -
Украшения с эмалью очищают ватным тампоном с нанесенной на него смесью зубного порошка с несколькими каплями нашатырного спирта. Не лишним будет и напоминание о правилах хранения ювелирных изделий. Во избежание появления на ювелирных украшениях темных пятен от прикосновения с влажной кожей, необходимо при снятии украшения сразу же протереть их сухой фланелью.
При выполнении различных хозяйственных работ, а также при соприкосновении с химикатами, рекомендуется снимать кольца, браслеты, и другие ювелирные изделия, что предохраняет их от повреждений и загрязнений.
Рекомендуется также снимать украшения при употреблении косметических средств, приготовленных на основе солей ртути и серы (сера легко образует с серебром сернистые соединения черного цвета). Темные пятна на серебряных изделиях оставляет йод.
Хранить ювелирные изделия следует в футлярах в сухом помещении. Чтобы серебряные вещи дольше сохраняли блеск, храните их так, чтобы они не касались друг друга и остальных украшений.
 Химическое и электрохимическое полирование Химическое и электрохимическое полирование принципиально отличаются от механического полирования. Обработанные этими методами полирования детали также приобретают блеск, привлекательную и гладкую поверхность. Химическое и электрохимическое полирование осуществляется растворами, содержащими активные добавки. Химическое полирование Химическое полирование заключается в том, что обрабатываемую деталь погружают на некоторое время в сосуд с химически активным раствором, где в результате возникающих химических и местных электрохимических процессов происходит растворение металла. Шероховатость поверхности уменьшается или совсем устраняется, при этом обработанная поверхность приобретает блеск. Все процессы химического полирования сопровождаются бурным выделением газов и паров кислот или щелочей. В процессе полирования рекомендуется перемешивать раствор или встряхивать детали в емкости. Это дает возможность устранять скопление пузырьков газов на отдельных участках деталей, так как пузырьки газов понижают качество полирования. Одним из главных преимуществ химического полирования является его простота. Для получения требуемого результата достаточно обрабатываемую деталь на несколько минут погрузить в соответствующий раствор, без применения электрического тока, без механического воздействия. Метод не требует сложного оборудования. К недостаткам такого полирования относится сложность корректирования (поддержание точных соотношений всех элементов в растворе путем добавления израсходованного элемента) растворов и малый срок их службы. Применяемые растворы чрезвычайно опасны для здоровья человека, и в домашних условиях без соответствующей подготовки проводить такое полирование нельзя. Блеск поверхности получается меньше, чем при электрохимическом полировании. Химическому полированию подвергаются в основном латунные или алюминиевые детали сложной конфигурации и небольших размеров, которые не требуют зеркального блеска. Электрохимическое полирование Электрохимическим полированием называется процесс отделки поверхности металлов, приводящий к уменьшению шероховатости и появлению зеркального блеска электрохимическим способом.Для осуществления электрохимического полирования обрабатываемую деталь, являющуюся анодом (т.е. электродом, соединенным с положительным полюсом источника тока), надо поместить в ванну с электролитом. Вторым электродом служат катоды, изготовленные из меди. На схеме показано протекание процесса электрохимического полирования. Благодаря специально подбираемому составу электролита и создаваемым условиям (образование пленки 2 повышенного сопротивления) растворение осуществляется неравномерно. В первую очередь растворяются наиболее выступающие точки 3 (выступы), вследствие чего шероховатость уменьшается, а затем исчезает, и поверхность детали становится гладкой и блестящей. Избирательное растворение торчащих элементов протекает с одновременным получением блеска. Удаление крупных выступов 3 называется макро-полированием, а растворение микроскопически малых неровностей 4 - микро-полированием. Если макро- и микро-полирование протекает одновременно, то поверхность приобретает гладкость и блеск. В ряде случаев эти качества могут быть несвязанными друг с другом, т.е. блеск может достигаться без сглаживания, а сглаживание - без блеска. В процессе электрохимического полирования на поверхности анода (полируемой детали) образуется окисная или гидроокисная пленка. Если эта пленка равномерно покрывает поверхность, то она создает условия, необходимые для протекания микро-полирования. Внешняя часть этой пленки непрерывно растворяется в электролите. Поэтому для успешного проведения процесса необходимо создания условий, в которых существовало бы равновесие между скоростями образования окисной пленки и скоростью ее химического растворения с тем, чтобы толщина пленки поддерживалась неизменной. Наличие пленки обусловливает возможность обмена электронами между полируемым металлом и ионами электролита без опасности местного разрушения металла агрессивным электролитом. Макро-полирование также является процессом, зависящим от наличия прианодной пленки. Будучи более толстой в углублениях и более тонкой на выступах, эта пленка способствует их ускоренному растворению, так как на выступах создается более высокая плотность тока, а электрическое сопротивление над ними меньше, чем над углублениями. Эффективность действия пленки увеличивается с повышением ее внутреннего сопротивления. Электролиты, содержащие соли слабодиссоциирующих кислот или комплексные соли, повышают сопротивление пленки. Кроме действия прианодной пленки на течение процесса электрохимического полирования влияют и другие факторы, в частности механическое перемешивание электролита (или движение анода), благоприятствующие утончению пленки за счет ее растворения или уменьшения толщины диффузионного слоя. Электролиты некоторых составов функционируют нормально только при нагреве. Общим правилом является то, что повышение температуры снижает скорость нейтрализации и повышает скорость растворения прианодной пленки. Существенными факторами, влияющими на течение процесса электрохимического полирования, являются также плотность тока и напряжение. В зависимости от состава электролита и обрабатываемого металла полирование ведут при режимах соответствующих различным участкам кривой. Так, полирование меди в фосфорной кислоте ведут при режиме предельного тока, когда не происходит образования кислорода. Рецепты ванн и режимы для химического и электрохимического полирования ВНИМАНИЕ!!! ВАННЫ для химического и электрохимического полирования ОЧЕНЬ ОПАСТЫ для здоровья, ОСОБЕННО ПРИ ВЫСОКИХ ТЕМПЕРАТУРАХ. Поэтому не пытайтесь делать этого дома, тем более если у вас нет необходимого навыка, знаний и оборудования!!! Химическое полирование деталей из углеродистой стали. Химическое полирование деталей из углеродистой стали можно выполнять в различных растворах. Один из них (в вес. %): 15-25% ортофосфорной кислоты, 2-4% азотной кислоты, 2-5% соляной кислоты, 81-60% воды. Режим работы: рабочая температура 80° С, выдержка 1-10 мин. В данном растворе производят также полирование нержавеющей стали. Химическое полирование деталей из стали выполнят также в следующем растворе: 25 г щавелевой кислоты, 13 г пергидроли, 0,1 г серной кислоты, до 1 л воды. Режим работы: рабочая температура 20° С, выдержка 30-60 мин. Химическое полирование деталей из нержавеющей стали. Химическое полирование деталей из нержавеющей стали марки Х18Н9Т выполняют в растворе следующего состава: 40 см3 азотной кислоты, 70 см3 соляной кислоты, 230 см3 серной кислоты, 10 г/л столярного клея, 6 г/л хлористого натрия, 6 г/л красителя кислотного черного. Режим работы: рабочая температура 65-70°С, выдержка 5-30 мин. Химическое полирование деталей из алюминия и его сплавов. Для полирования мелких алюминиевых деталей используют следующий состав раствора: 60 см3 ортофосфорной кислоты, 200 см3 серной кислоты, 150 см3 азотной кислоты, 5 г мочевины. Режим работы: рабочая температура 100- 110° С, выдержка 15-20 с. Полирование деталей из алюминиево-магниевого сплава АМг производят в одном из растворов следующего состава: 500 или 300 см3 ортофосфорной кислоты, 300 или 450 см3 серной кислоты (аккумуляторной), 150 или 170 см3 азотной кислоты. Химическое полирование деталей из меди и, ее сплавов. Химическое полирование деталей из меди и ее сплавов выполняют в следующем растворе: 800 см3 серной кислоты; 20 см3 азотной кислоты; 1 см3 соляной кислоты; 200 см3 пергидроли; 20-40 см3 хромового ангидрида. Режим работы: рабочая температура 20-40°С, выдержка до 1-2 мин. Может быть также использован раствор: 250-270 см3 серной кислоты, 250-270 см3 азотной кислоты, 10-12 см3 нитрита натрия. Режим работы: рабочая температура 30-40° С, выдержка 1-3 мин. Химическое полирование деталей из никеля. Для химического полирования деталей из никеля используют раствор (в вес. %) 45-60% ортофосфорной кислоты, 15-25% серной кислоты, 8-15% азотной кислоты, 10-20% соды. Режим работы: рабочая температура 65-70° С, выдержка 0,5-1 мин. Электролитическое полирование деталей из углеродистой стали. Наиболее популярным является так называемый универсальный электролит для полирования деталей из черных и цветных металлов. Его состав следующий (в вес. %): 65% ортофосфорной кислоты, 15% серной кислоты, 6% хромового ангидрида, 14% воды. Режим работы: рабочая температура 70-90° С, анодная плотность тока 40-80 а/дм2, напряжение 6-8 в, выдержка 5-10 мин. Электролитическое полирование деталей из нержавеющей стали. Детали из нержавеющей стали (хромоникелевой и хромоникельмолибденовой) полируют в растворе (в вес. %): 65% ортофосфорной кислоты, 15% серной кислоты, 5% хромового ангидрида, 12% глицерина, 3% воды. Режим работы: рабочая температура 45-70°С, анодная плотность тока 6-7 а/дм2, напряжение 4,5-6в, выдержка 4- 30 мин (для штампованных деталей 4-6 мин, для деталей после сварки или термической обработки 10-12 мин, для литых отпескоструенных деталей из стали Х18Н9Т около 30 мин). Электролитическое полирование деталей из алюминия и его сплавов. Для полирования деталей из алюминия и сплавов АМг и АМц хорошо зарекомендовал себя электролит, следующего состава (в вес. %): 65-70% ортофосфорной кислоты, 8-10% хромового ангидрида, 20-27% воды. Режим работы: рабочая температура 70-80° С, плотность тока в свежеприготовленном растворе 10-30 а/дм2, в растворе насыщенном солями 10-20 а/дм2. Выдержка 5 мин и более. Реверсирование при применении свежеприготовленного раствора tа-10 сек, tк - 2 сек; при применении раствора насыщенного солями, tа - 10 сек, tк - 5 сек. Для полирования деталей из дюралюминия Д16-Т рекомендуется следующий состав раствора (в вес. %): 40% серной кислоты, 45% ортофосфорной кислоты, 3% хромового ангидрида, 11% воды. Режим работы: рабочая температура 60-80° С, анодная плотность тока 30-40 а/дм2, напряжение 15-18 в, выдержка - несколько минут. Электролитическое полирование деталей из никеля и никелевых покрытий. Для полирования деталей из никеля рекомендуется раствор: 1200 г/л серной кислоты, 120-150 г/л ортофосфорной кислоты, 15-20 г/л лимонной кислоты. Режим работы: рабочая температура 20-30° С, анодная плотность тока 30-50 а/дм2, выдержка до 1 мин. Для полирования применяют также 70%-ный раствор серной кислоты. Анодная плотность тока 40 а/дм2, температура 40°С, продолжительность процесса 30 сек. Электролитическое полирование деталей из меди и ее сплавов. Для полирования этих деталей применяют следующий электролит: 1200 г/л ортофосфорной кислоты, 120 г/л хромового ангидрида. Режим работы: рабочая температура 20-30°С, анодная плотность тока 35-50 а/дм2, выдержка 0,5-2 мин. Применяют также однокомпонентный раствор ортофосфорной кислоты при температуре 18-25°С; анодная плотность тока для деталей из меди 1,6 а/дм2, для деталей из медных сплавов 0,8-1 а/дм2, выдержка 10-20 мин. Литература: Бартл Д. Мудрох О. Технология химической и электрохимической обработки поверхности металлов. - М., 1961. Гарбер М.И. Декоративное шлифование и полирование. - М., 1964. Жаке П. Электрохимическое и химическое полирование. - М., 1959 Масловский В.В. Дудко П.Д. Полирование металлов и сплавов. - М.,1974. Пяндрина Т.Н. Электрохимическая обработка металлов. - М., 1961. Тегарт А.С. Электролитическое и химическое полирование металлов. - М., 1957. Щиголев П.В. Электрохимическое и химическое полирование металлов. - М., 1958.
на этом месте ваша рекламма тел. 922-722
друзья сайта:
http://volgogradzoloto.narod.ru/
друзья сайта:
17 ноября 2010
17.11.2010 - В Британии разработан новый способ создания многоцветных узоров на поверхности металлов Команда…
17 ноября 2010
Избирательный растворитель отделяет золото от палладия Благородные металлы, такие как платина, паллади…
16 декабря 2010
Предлагаемое нами оборудование для хромирования представляет собой специальную передвижную установку для …
16 декабря 2010
у нас золото в эстафете на чемпионате мира в Дубай 4*200 короткая вода мужчины!!!!(Лобинцев ,Изотов ,Логунов , Сухо…
28 декабря 2010
IV МЕЖДУНАРОДНЫЕ СОРЕВНОВАНИЯ ПО ПЛАВАНИЮ «КУБОК ВЛАДИМИРА САЛЬНИКОВА» В течение двух дней 28 и 29 декабря в …
14 января 2011
Волгоград попал в WikiLeaks Среди огромного количества секретных документов, выложенных на скандально …
14 января 2011
С 15 января запрос через мобильный телефон поможет получить полное расписание трамваев и троллейбусов.Услуга…
16 января 2011
Обычно твердость и прочность материала не сочетаются, но исследователи из Лаборатории Беркли и Калифорнийс…
20 января 2011
Здание волгоградского ЦУМа хотят освободить от торговцев. Вместо этого помещение планируют использовать д…
|